Spis treści
- Automatyzacja produkcji a Przemysł 4.0
- Automatyzacja produkcji z wykorzystaniem technologii BIM
- Automatyzacja produkcji – Internet Rzeczy i cyfrowa chmura
- Automatyzacja produkcji – jak zmienić zakład w bardziej wydajny i nowoczesny?
- Automatyzacja produkcji oparta na zintegrowanej platformie wymiany danych
- Automatyzacja produkcji z zastosowaniem inteligentnych maszyn i urządzeń
Automatyzacja produkcji z wykorzystaniem sterowanych cyfrowo maszyn pracujących w ciągu technologicznym zdecydowanie ograniczyła zakres pracy ludzkiej. Zautomatyzowana produkcja okien i drzwi ma centralny system zarządzania, dzięki czemu element okna lub drzwi na każdym etapie jest identyfikowany i przypisywany do konkretnego produktu oraz klienta. W ten sposób eliminowane są pomyłki i wady wyrobów gotowych przy jednoczesnym wzroście wydajności zakładu. Współczesny rynek stawia przed producentami stolarki kolejne wyzwanie. Krótki czas życia produktów i usług wymaga częstych zmian profilu wytwórczego oraz szybkiego dostosowania się do ciągle rosnących oczekiwań konsumentów. Długie serie są więc wypierane przez krótkie czy nawet produkcję jednostkową. Wymagana jest większa elastyczność wytwarzania oraz indywidualizacja zamówień. Masową produkcję okien i drzwi ma zastąpić masowa personalizacja, co umożliwiają najnowsze technologie, wymieniające się informacjami i tworzące jeden organizm, docelowo działający bez udziału człowieka. Rozpoczął się w ten sposób kolejny etap technologicznego rozwoju, określany jako czwarta rewolucja techniczna lub Przemysł 4.0.
Termin „rewolucja przemysłowa” odnosi się do przełomowych osiągnięć technologicznych, których efektem były ważne przemiany w strukturze i organizacji produkcji. Do pierwszej rewolucji doszło w XVIII wieku wskutek upowszechnienia napędu parowego. Przyczyniła się ona do powstania przemysłu, rozwoju transportu kolejowego i morskiego. Druga rewolucja zaczęła się pod koniec XIX wieku i była skutkiem wynalezienia silnika elektrycznego i spalinowego oraz produkcji na linii montażowej. Za prekursora nowej organizacji pracy uznawany jest Henry Ford, który w 1913 roku zastosował ruchomą taśmę do montażu samochodów w swojej fabryce w Highland Park. W latach 70. XX wieku miała swój początek trzecia rewolucja przemysłowa. Była wynikiem rozwoju komputerów oraz informatyzacji i spowodowała powszechną automatyzację w przemyśle. Od tego czasu znacząco przyspieszył proces ograniczania udziału pracy ludzkiej w produkcji.
Automatyzacja produkcji a Przemysł 4.0
Obecnie trwa czwarta rewolucja przemysłowa, w dużej mierze będąca rozwinięciem trzeciej. Oznacza dalszą automatyzację produkcji, z wykorzystaniem samouczących się, inteligentnych maszyn, najnowszych rozwiązań w zakresie komunikacji i gromadzenia danych, optymalizujących procesy wytwórcze. Główną ideą Przemysłu 4.0 jest personalizacja i dostosowanie działania przedsiębiorstw do indywidualnych potrzeb klienta. Firma, która nie będzie w stanie zaproponować nabywcy produktu zgodnego z jego oczekiwaniami, może zacząć tracić udziały w rynku. Wyroby posiadające nietypowe cechy, które czynią je unikatowymi, muszą mieć konkurencyjną cenę, a czas ich wytworzenia nie może być znacząco dłuższy niż wyrobów standardowych. Jednocześnie należy to osiągnąć bez zwiększania kosztów jednostkowych oraz spadku wydajności.
Zmiany technologiczne dotyczą wszystkich etapów życia produktu, od projektowania aż po sprzedaż i serwis. Klient staje się aktywnym uczestnikiem tworzenia, może swoje oczekiwania zobrazować, umieścić w internetowej chmurze i zamówić towar w sklepie internetowym. Dzięki aplikacji na smartfon i wizualizacji w rozszerzonej rzeczywistości ma nawet szansę zobaczenia produktu w swoim domu. Takie możliwości oferuje już wielu producentów osłon okiennych i tarasowych. Poza tym na rynku są dostępne cyfrowe ekspozytory, które zastępują fizyczne okna i drzwi. Można w nich zmienić wszystko w czasie rzeczywistym oraz pokazać każdą dostępną opcję produktu.
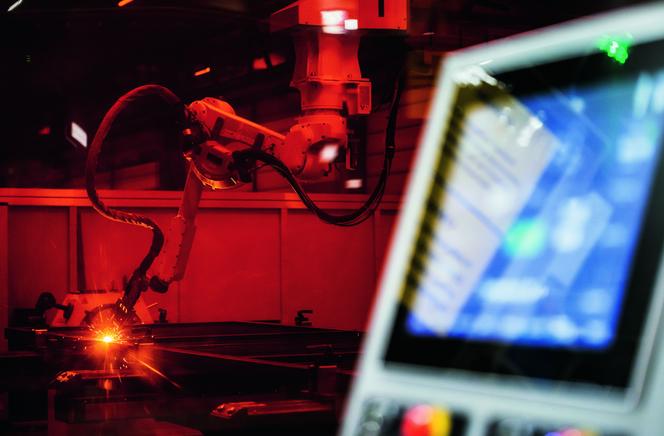
i
Automatyzacja produkcji z wykorzystaniem technologii BIM
Architekci mają do dyspozycji cyfrowe katalogi elementów do projektowania trójwymiarowego. Technologia określana jako BIM (ang. Building Information Modeling) pozwala na cyfrowe modelowanie budynku. Trójwymiarowy model ma wszystkie parametry rzeczywistego obiektu. Stolarkę do takiego projektu pobiera się z biblioteki udostępnionej przez producenta systemu bądź gotowego produktu. Zamówienie okna czy drzwi również wykonuje się elektronicznie wprost z modelu cyfrowego, co eliminuje pomyłki. Po oddaniu budynku do użytku model jest przydatny przy zarządzaniu obiektem, w konserwacji i serwisowaniu. Wykonanie cyfrowego projektu zaakceptowanego czy nawet w całości opracowanego przez klienta to dopiero pierwszy krok. Kolejne można łatwo zautomatyzować. System zarządzający zakładem natychmiast sprawdzi, jakie elementy i surowce są potrzebne do wykonania zlecenia, i je zamówi. Następnie zaplanuje produkcję oraz określi termin dostawy gotowego produktu. Sztuczna inteligencja doskonale potrafi zastąpić człowieka w działaniach wymagających kompetencji obliczeniowych oraz przetworzenia licznych informacji. Wykorzystując samouczące się algorytmy, fabryka przeprowadzi cały proces automatycznej produkcji z minimalnym udziałem ludzi lub w pełni autonomicznie.
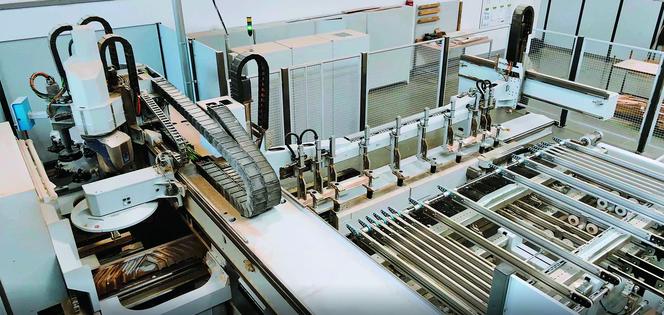
i
Automatyzacja produkcji – Internet Rzeczy i cyfrowa chmura
Filarem czwartej rewolucji przemysłowej jest automatyzacja wymiany danych między urządzeniami pracującymi w firmie oraz dostawcami i klientami. Maszyny wyposażone w czujniki komunikują się między sobą i korzystają ze wspólnych danych, tworząc w ten sposób swoje „sieci społecznościowe”. Są częścią większej, powszechnej sieci określanej jako Internet Rzeczy (ang. Internet of Things, IoT). Zastąpienie tradycyjnych metod pozyskiwania danych aplikacjami opartymi na IoT pozwala prowadzić dokładniejsze odczyty i zaoszczędzić czas. Tym samym efektywniej wykorzystywać zasoby ludzkie i maszyny, a więc zmniejszyć koszty. Elementem nieodłącznie związanym z Internetem Rzeczy jest pojęcie dużego zbioru danych (ang. Big Data). To zestaw danych pozyskiwanych, magazynowanych oraz przetwarzanych przez urządzenia pracujące w obrębie IoT.
Możliwości zakładów zajmujących się produkcją okien i drzwi są jednak często niewystarczające, aby poradzić sobie z tym wyzwaniem, dlatego korzystają one z usług dostawców oferujących przetwarzanie i przechowywanie informacji w chmurach obliczeniowych. Muszą oni zapewnić odpowiednie zabezpieczenie danych i zminimalizowanie ryzyka utraty czy ingerencji osób niepożądanych. Dodatkowym wsparciem dla działów utrzymania ruchu jest zdalny serwis proponowany przez dostawców maszyn. Dzięki połączeniu internetowemu mają oni możliwość diagnozowania stanu urządzeń i zdalnej naprawy usterek. Mogą też skorygować parametry pracy maszyny na odległość, podpowiedzieć rozwiązanie problemu, dostarczyć odpowiednie części czy wysłać serwisanta na miejsce. Również do serwisowania maszyn używa się rozszerzonej rzeczywistości. Na przykład inteligentne okulary z wbudowaną kamerą wideo, wyposażone w połączenie bezprzewodowe pozwalają serwisantowi na dwukierunkową komunikację bez użycia rąk.
i
Automatyzacja produkcji – jak zmienić zakład w bardziej wydajny i nowoczesny?
U wielu przedsiębiorców zajmujących się produkcją okien i drzwi wdrożenie rozwiązań Przemysłu 4.0 wynika z konieczności dostosowania się do zmieniających się wymogów globalnego rynku. Chodzi przede wszystkim o umożliwienie automatyzacji produkcji okien i drzwi w małych seriach, o nietypowych cechach geometrycznych lub funkcjonalnych, zwiększenie wydajności, niezawodności, lepsze wykorzystanie maszyn, minimalizację przestojów – w efekcie o obniżenie kosztów produkcji.
Dodatkowym czynnikiem przemawiającym za zmianami jest trwały niedobór pracowników, niedopasowanie ich kompetencji oraz systematycznie rosnące wymagania płacowe. Nowa sytuacja powstała wraz z rozprzestrzenieniem się wirusa SARS-CoV-2. Zagrożenie lockdownem czy kwarantanną sprawia, że konieczność automatyzacji i robotyzacji staje się dziś jeszcze pilniejsza. Rozpoczęcie i przeprowadzenie procesu transformacji do Przemysłu 4.0 wymaga dużej świadomości i motywacji. Wszystko zależy od profilu działalności, wielkości zakładu, stanu kontroli wytwarzania, istniejącej infrastruktury oraz sieci wymiany danych. W wysoce zautomatyzowanych zakładach wejście w strefę Przemysłu 4.0 może być naturalnym rozwinięciem dotychczasowej organizacji produkcji okien i drzwi – w oparciu o pracujące już maszyny sterowane cyfrowo oraz programy zarządzające magazynem, produkcją i sprzedażą.
W przypadku małego zakładu stolarskiego korzystającego z obsługiwanych ręcznie maszyn pojawia się już więcej pytań i wątpliwości. Dotyczą często spraw strategicznych, a odpowiedzi wymagają dogłębnej analizy rynku, oceny możliwości sukcesji bądź szacowanej wartości firmy w razie jej sprzedaży. Podstawowe pytanie brzmi: czy firma potrzebuje wdrożenia elementów Przemysłu 4.0 i co będzie, jeśli tego nie zrobi? Należy ustalić, jakie będą rzeczywiste korzyści dla firmy oraz jakie rozwiązania faktycznie są niezbędne. Ile będą kosztować i w jakiej perspektywie czasowej trzeba je wdrożyć? W jaki sposób gromadzić dane, jak je wykorzystywać i zabezpieczyć przed dostępem osób niepożądanych?
Wejście w rozwiązania z dziedziny Przemysłu 4.0 musi być przemyślanym projektem, z dokładnym podziałem czynności na wykonywane przez ludzi i maszyny. Nie polega ono tylko na zakupie pojedynczego urządzenia, np. superwydajnego centrum obróbczego CNC. To musi być sprawnie działający system oparty na inteligentnych maszynach oraz programie zbierającym i analizującym dane. Takie przejście technologiczne wymaga znacznych inwestycji. Co prawda są one w zasięgu możliwości nawet średniej wielkości przedsiębiorstw, ale mogą stanowić znaczne obciążenie. Nagrodą jednak za dobrze przeprowadzone wdrożenie narzędzi Przemysłu 4.0 jest redukcja kosztów produkcji i utrzymanie lub wzmocnienie pozycji na rynku.
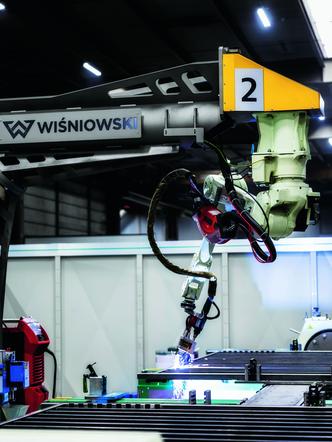
i
Automatyzacja produkcji oparta na zintegrowanej platformie wymiany danych
Systemy wspierające zarządzanie klasy ERP i MES przyczyniają się do zwiększenia efektywności produkcji okien i drzwi o 15–25% i zredukowania czasu przestoju maszyn o 30–50%. Nie rozwiązują jednak wszystkich problemów kadr zarządzających produkcją. Dlatego oprogramowania dla Przemysłu 4.0 mają bardziej kompleksowy charakter. Zbierają i przesyłają dane do systemów zarządzania przedsiębiorstwem, programów księgowych, magazynowych czy sprzedażowych. Wymieniają informacje z maszynami do produkcji stolarki: piłami lub centrami obróbczymi, a także z sortownikami szyb, robotami i automatycznymi magazynami. Mogą być również wykorzystywane do projektowania, wycen, rozliczeń, zamówień i przygotowania produkcji. Taki system przetwarza zebrane dane w celu optymalizacji wydajności lub kosztów zakładowych. Może wykrywać i rozwiązywać problemy związane ze zużyciem maszyn, niewłaściwymi komponentami, kontrolować jakość produkcji, a nawet komunikować się z klientami. Na podstawie odczytów parametrów maszyn oraz urządzeń monitorujących ich stan i wydajność, analizowanych w połączeniu z danymi archiwalnymi, można z wyprzedzeniem wykryć oznaki zbliżającej się awarii. Maszyny planują również okresy między przeglądami konserwacyjnymi i ewentualne naprawy, wykorzystując do tego przerwy produkcyjne i weekendy.
Programy zarządzające korzystają z internetowej chmury, dzięki czemu dane są dostępne dla każdego uprawnionego, niezależnie od miejsca, w którym się znajduje. W każdej chwili może on zobaczyć, jak wygląda produkcja i co działo się wcześniej. Docelowo firmy działające według zasad Przemysłu 4.0 powinny mieć jedną automatycznie aktualizowaną platformę informacyjną, zawierającą wszystkie niezbędne dane. Od kilku lat w różnych dziedzinach przemysłu powstają autonomiczne fabryki, samodzielnie sterujące wszystkimi procesami produkcyjnymi. System zarządzający jest w stanie działać niemal bez ingerencji człowieka, bez planistów i kierowników. W czasie rzeczywistym podejmuje optymalne decyzje dotyczące kolejności realizacji i doboru zasobów dla poszczególnych czynności technologicznych. Każdy pracownik, po zgłoszeniu się do systemu, otrzymuje polecenie realizacji czynności optymalnej w momencie jej wydania. Do jego komunikacji z systemem wykorzystywane są różne technologie: terminale, tablety, smartfony, wyświetlacze sterowników maszyn, komputery osobiste, a w najbliższej przyszłości również rozszerzona rzeczywistość i polecenia głosowe. System jest szybszy i efektywniejszy od zarządzania ludzkiego, dzięki czemu produktywność rośnie nawet o 20–30%. Jednocześnie gromadzony jest szereg danych pozwalających na szczegółową analizę procesów oraz porównanie parametrów pracy poszczególnych zasobów w dowolnym okresie.W przyszłości taki system będzie mógł zarządzać ludźmi i maszynami bez ingerencji kierownictwa fabryki, a ponadto samodzielnie reagować w przypadku sytuacji zagrażających wykonaniu planu czy nadzorować obieg dokumentów i informacji w ramach firmy. Tym samym powstanie w pełni autonomiczna fabryka. Branża okien i drzwi jest bardzo podatna na takie innowacyjne zarządzanie. Jak informuje dostawca polskiego systemu IPO, obecnie prowadzone są rozmowy z dwiema fabrykami okien na temat wdrożenia autonomicznego zarządzania.
Automatyzacja produkcji z zastosowaniem inteligentnych maszyn i urządzeń
Podstawą nowoczesnego zakładu z zastosowaniem automatyzacji produkcji okien lub drzwi są inteligentne maszyny. Do standardowego wyposażenia fabryki produkującej okna i drzwi należą sterowane numerycznie piły, wielozadaniowe centra obróbcze, zgrzewarki czterogłowicowe oraz wielonarzędziowe oczyszczarki naroży. Te najbardziej zaawansowane mają też zautomatyzowane okuwanie, transport wewnętrzny oraz magazyn szyb.
Coraz bardziej inteligentne i samodzielne w działaniu maszyny umożliwiają wzrost produkcji nawet o 30% oraz spadek jej kosztów o 25%. Na przykład obrabiarki sterowane numerycznie mają automatyczny system wymiany narzędzi – same odkładają na stojak w magazynie „stare” narzędzia oraz zgodnie z programem obróbki rozpoznają i pobierają „nowe”. Dzięki temu skraca się czas przezbrajania i przyspiesza obróbka wymagająca użycia wielu narzędzi. Możliwości centrów obróbczych dodatkowo poszerzają agregaty CNC, niewielkie urządzenia z systemem przekładni zębatych. Pozwalają wykonywać na centrach czteroosiowych takie same obróbki jak na bardziej rozbudowanych maszynach. Aby sprostać zapotrzebowaniu na inteligentne rozwiązania w przemyśle, najnowsze wersje agregatów wyposażane są w czipy, które obserwują i zapisują parametry pracy. Informacje przekazywane są bezprzewodowo na telefon lub tablet operatora. Kontrola odbywa się na bieżąco w poszczególnych etapach pracy lub w ustalonych okresach eksploatacji urządzenia. Dzięki stałemu dostępowi do informacji dotyczących godzin pracy agregatu, jego temperatury, obrotów oraz poziomu wibracji na wrzecionie możliwe jest zaplanowanie koniecznych przestojów bądź podjęcie decyzji o przekazaniu do serwisu jeszcze przed awarią urządzenia. Dostępna jest też funkcja awaryjnego wyłączenia, gdy parametry pracy są niewłaściwe. Agregat CNC z czipem może być połączony bezpośrednio z działem serwisu producenta, który w porozumieniu z klientem ustala terminy przeglądów serwisowych.
Sterowane cyfrowo zgrzewarki mają zaprogramowane wszystkie parametry, takie jak temperatura, czas podgrzewania, ciśnienie i czas łączenia. Po włożeniu profili i uruchomieniu procesu automatycznie ustawiają je odpowiednio do rodzaju ramy i szerokości spoiny. Wystudzone zgrzewy zostają oczyszczone na automatycznej oczyszczarce wyposażonej w kilkanaście narzędzi i zaprogramowanej do kompletnej obróbki profilu. Po rozpoznaniu obrabianego elementu maszyna samoczynnie dobiera narzędzia i program.
Ciekawym rozwiązaniem, zbieżnym z ideą Przemysłu 4.0, jest drukowanie okien. Pierwsze okna z drukarki 3D są już w sprzedaży na rynkach skandynawskich. Powstają z biokompozytu, czyli polimeru zmieszanego z niekopalnymi surowcami naturalnymi, jak odpady drewna, korek, słoma czy włókna konopi. W porównaniu z oknem drewnianym proces produkcyjny jest krótszy o 50%. Poza tym ramę z biokompozytu łatwo można poddać recyklingowi i przetworzyć na nowy produkt.